Process Management Library
Foundations
Business Process Management
Related frameworks and ideas
What is 5S methodology? How to implement 5S in the office?
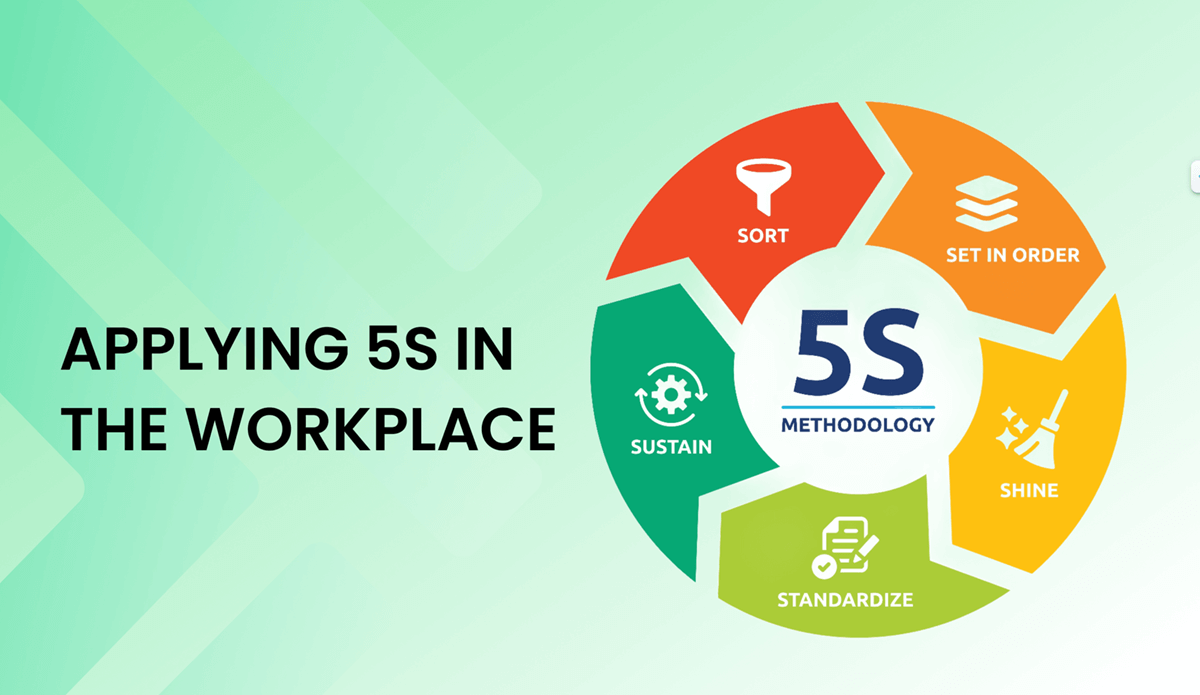
Did you know that office space and work efficiency are closely connected? The more cluttered your workspace, the more likely your productivity will drop.
From a logical perspective, this makes perfect sense: When your desk isn’t organized, just finding documents and supplies can take up a lot of time. According to global research by IDC, office workers spend up to 2 hours a week searching for documents (both physical and digital).
But the consequence of a messy workspace doesn’t stop there. Research by psychologist Dr. Libby Sander from Bond University shows that the physical environment significantly affects employees’ perceptions, emotions, and behavior. Negative psychological conditions, such as stress and anxiety, can be partly caused by clutter. These factors reduce your ability to focus, lower your performance, and cost businesses up to $190 billion annually in lost productivity.
It's time to recognize the downside of clutter in your work life and start cleaning it up with 5S right away!
What is 5S?
5S is a 5-step workplace organization system that eliminates waste while prioritizes efficiency, cleanliness, order, and safety. Each “S” represents a part of the five-step process aimed at enhancing a business's overall operations. It is an integral part of lean management methodology.
- Seiri (Sort): Eliminate unnecessary items to create a clean and organized workspace.
- Seiton (Set in order): Arrange and organize necessary items for easy access and use.
- Seiso (Shine): Clean the workspace, including machines and equipment.
- Seiketsu (Standardize): Maintain cleanliness and organization by upholding and promoting standards and procedures.
- Shitsuke (Sustain): Foster a culture of discipline and personal responsibility, continuously improving the established standards.
The origin of 5S
This continuous performance improvement program originated in Japan and was developed and widely implemented in the country's industry from the late 1950s to the early 1960s.
5S was first applied in manufacturing, particularly in automotive factories and businesses such as Toyota. 5S is considered an essential part of the "Toyota Production System," which has been successfully implemented and spread globally to this day.
Initially, the method was called "4S" and consisted of four main steps: Seiri (Sort), Seiton (Set in order), Seiso (Shine), and Seiketsu (Standardize). Later, the fifth step, Shitsuke (Sustain), was added to complete the 5S model.
Today, 5S is not only trusted in the manufacturing sector but has expanded into various industries such as services, technology, healthcare, and education as part of their operational standards.
Difference between 5S and Kaizen
Both 5S and Kaizen originated in Japan with the ultimate goal of improving work processes, avoiding unnecessary waste in operations, and increasing overall productivity. However, these two models have some distinct differences:
Breakdown of the 5S methodology
Seiri – Sort
This is probably the toughest step in the 5S method, where you need to learn how to remove anything unnecessary from your workspace. This could include tools, documents, or personal items. If you haven’t used these items in the past 12 months or they don't directly support your current tasks, it’s time to say goodbye to them.
Recycling (or discarding) even the smallest unused items will help declutter your workspace, making it more efficient for the next step.
Seiton – Set in Order
Sakichi Toyoda, the founder of Toyota, was particularly fond of a famous quote by English author Samuel Smiles: “A place for everything, and everything in its place.” This idea is the heart of the second step in the 5S system.
After sorting and keeping only the essentials, the next task is to organize everything in a way that’s logical and easy to find. The goal here is to maintain a flow state during your work.
Additionally, all tools and equipment should be placed in visible and accessible spots in the workspace. This follows the visual management principle, making it easy for anyone nearby to see, grab, and return items quickly.
“A place for everything, and everything in its place.”
- Samual Smiles
Seiso – Shine
Along with being organized, a standard 5S workspace also needs to be kept clean. Maintaining cleanliness not only promotes health and safety but also boosts work efficiency.
To effectively keep your space clean, develop the habit of tidying up after using items and removing trash immediately. Schedule regular cleaning times, spending just 3-5 minutes at the start of each day to tidy up and reset your workspace to avoid clutter.
It’s important to note that cleanliness isn’t solely the responsibility of cleaning staff, every employee should take responsibility for maintaining a clean working environment.
Seiketsu – Standardize
After completing the first three steps, your workplace may look tidy, clean, and organized. But how long will it stay that way?
Seiketsu is about regularly maintaining and standardizing the first three steps of the 5S method. To ensure long-term success, businesses need to set clear standards outlining individual responsibilities, methods, and the frequency of implementing 5S in specific areas.
Reluctance to take on these responsibilities can lead to negative outcomes. Therefore, 5S is only successful when employees consistently follow and develop a sense of responsibility through this Standardization step.
Shitsuke – Sustain
This is the core of the 5S system, and while it’s the final step, it’s a never-ending process. It acts as the driving force that keeps the 5S system running smoothly. This step also reflects the strong sense of personal discipline, which is a hallmark of Japanese culture.
At this stage, the company creates incentives and recognition programs to encourage full participation and commitment from all employees in sustaining 5S practices. Over time, each employee develops the discipline to maintain an organized work style and a high sense of responsibility.
Benefits of the 5S model
- Increased work efficiency: A “5S compliant” work environment allows employees to easily access and use necessary tools, documents, and equipment. Instead of wasting time searching for items, they can fully focus on their tasks, increasing work efficiency and reducing the time needed to complete their work.
- Reduced waste: The 5S method eliminates unnecessary items and optimizes the use of the workspace. This helps reduce waste in terms of time, materials, and human resources. As a result, not only are production costs lowered, but it also enhances the company's profits and competitive edge in the market.
- Improved product/service quality: A clean and organized work environment significantly reduces errors in the production process or service delivery. Additionally, when everything is in its proper place and easy to access, it builds customer trust and loyalty.
- Enhanced workplace safety: 5S reduces the risk of accidents and injuries caused by cluttered or unsafe environments. This not only protects employees' health and safety but also minimizes legal risks and costs for the company.
- Boosted employee morale: When employees see their workspace clean, organized, and well-structured, they feel valued and are more motivated to perform better. This fosters positive work attitudes and self-discipline, creating a dynamic work culture within the organization.
How to combine 5S with other models
What is 3D 5S?
3D 5S is a business management principle popular in Japan and increasingly recognized by companies worldwide. It focuses on three key principles that leaders must follow to effectively guide and manage a business: Directing, Discussing, and Delegating.
Implementing 5S doesn’t always go as smoothly as leaders might expect, which is why the 3D model is applied. To ensure that every individual in an organization takes the 5S seriously, especially in the early stages of its adoption, 3D is essential.
This means that the leader must set the direction, guide employees on the specific tasks, and explain how to achieve the best results. Afterward, they should delegate tasks and responsibilities and set clear standards to start the implementation process.
What is Kaizen 5S?
Kaizen, a Japanese term meaning "continuous improvement," is a management philosophy and working method developed in Japan. It emphasizes the pursuit of ongoing, small improvements within an organization.
Kaizen 5S combines the continuous improvement philosophy of Kaizen with the workplace management principles of 5S. The goal is to create a work environment that constantly improves and optimizes while maintaining organization, cleanliness, and efficiency in daily tasks. This synergy boosts productivity, quality, and flexibility within the organization.
Implementing 5S lays a strong foundation for rolling out Kaizen activities, enabling organizations to continuously improve, enhance quality, boost performance, and increase competitiveness.
6 steps to implement 5S
Step 1: Assess the current situation
Implementing the 5S method requires careful planning and execution. Before you begin, take a look at the current state of your business:
- Do people at your workplace struggle to find documents or files, whether in physical or digital format?
- Are there loose or tangled electrical cables around the workspace?
- Are there file folders, drawers, or cabinets without labels, or containing unmarked, hard-to-identify items?
- Do unnecessary items take up space in important work areas?
- Are there papers that are not in use and gathering dust at your workplace?
- Do employees know how to organize their workspace neatly, and are they fully aware of their roles and responsibilities?
If you answered "Yes" to any of these questions, then the 5S method is exactly what you need!
Step 2: Build an action plan
The 5S process starts with creating a detailed action plan. The organization needs to set clear goals for the implementation of 5S and lay out specific steps to achieve those goals.
An effective plan should identify:
- The tools and resources required
- Specific activities and expected timelines for each step
- Estimated budget for each step of the roadmap
- Roles and responsibilities for each team member: managers, supervisors, and employees responsible for tasks A, B, C, etc.
Simultaneously, the company should communicate the 5S method and the implementation plan within the organization to ensure all employees understand the concept and are ready to participate.
Step 3: Training and instruction
Training and guidance are crucial parts of the 5S implementation process. This step helps build a knowledge foundation for employees and fosters commitment to the 5S process.
Before beginning, employees need to be trained on the purpose, goals, and steps of the 5S process. Following this, training will focus on applying 5S in the specific work environment of the company, department, or task.
Training can be conducted through in-person sessions, online classes, instructional videos, or study materials.
Step 4: Execution
Once the plan and roadmap are in place, the organization can begin executing 5S. Each step must be carried out according to the plan and schedule, with management support to ensure success and effectiveness.
During execution, companies should address violations and recognize and reward employees who excel in their roles.
Step 5: Evaluation and improvement
The 5S implementation process should be evaluated to identify strengths, weaknesses, and areas for improvement. Feedback from employees and managers is essential for enhancing the 5S process and promoting continuous development.
The company can conduct review meetings, employee surveys, interviews, or use performance evaluation tools. Based on the feedback, improvements can be made to refine the 5S process and ensure continuous enhancement.
Step 6: Sustain the practice
Finally, the 5S process must be maintained and continuously practiced over time. This involves periodic checks, adherence to established standards, and resolving issues as they arise.
Sustaining the practice may include setting up a schedule for regular inspections and maintenance and creating a feedback system to handle complaints from employees or customers.
It’s more than just organizing things!
Implementing 5S is more than just organizing things; it’s about creating a culture of continuous improvement where every employee takes responsibility for their environment. Great breakthroughs often stem from the smallest details, and the relationship between productivity and the work environment follows this same principle. Over time, the positive impact of these small changes will accumulate, driving significant improvements in overall performance.
The lifecycle of effective Business Process Management (BPM)
On this page
- What is 5S?
- The origin of 5S
- Difference between 5S and Kaizen
- Breakdown of the 5S methodology
- Seiri – Sort
- Seiton – Set in Order
- Seiso – Shine
- Seiketsu – Standardize
- Shitsuke – Sustain
- Benefits of the 5S model
- How to combine 5S with other models
- What is 3D 5S?
- What is Kaizen 5S?
- 6 steps to implement 5S
- Step 1: Assess the current situation
- Step 2: Build an action plan
- Step 3: Training and instruction
- Step 4: Execution
- Step 5: Evaluation and improvement
- Step 6: Sustain the practice
- It’s more than just organizing things!