Process Management Library
What is Kanban? A guide to apply Kanban to manage your work projects
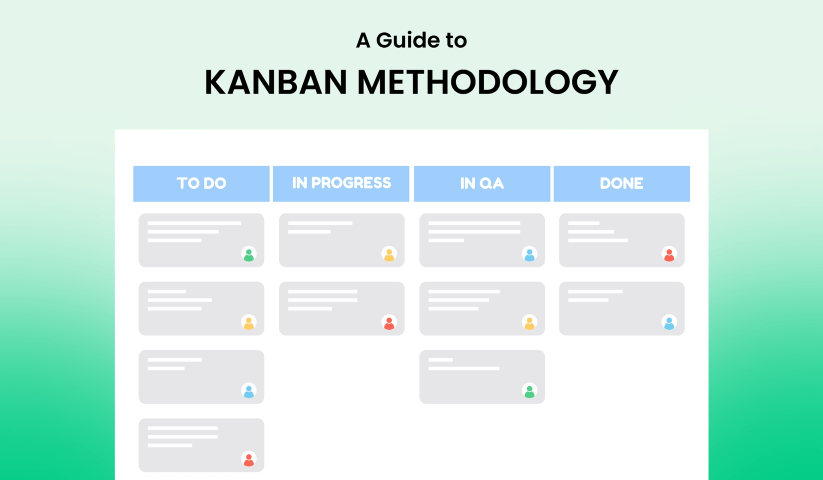
Project and task management can often become complex and challenging in the modern work environment. This is why globally recognized management methodologies are studied, upgraded, and applied extensively. Among these, Kanban stands out as a key that helped Toyota become one of the leading automobile manufacturers in the world.
This article will explore Kanban's core principles, how to implement It, and strategies for optimizing your workflow using the Kanban model.
1. What is Kanban?
Definition of Kanban
Kanban is a Japanese term first used by Toyota in the automotive industry. In Japanese, "Kanban" is derived from "kan" (visual) and "ban" (card or board), which can be simply understood as an "information board."
The Kanban model is a visual tool for tracking tasks, allowing project team members to see where each task stands within the workflow. The simplest way to implement this is to use whiteboards with colored sticky notes to describe and manage work processes.
The history of Kanban
In the late 1940s, Toyota faced a crisis due to intense domestic and international competition. To address this challenge, engineer Taiichi Ohno proposed a method to improve and optimize the company's production system. This method was initially called "Just-in-Time" (JIT) and was designed to meet production timelines based on customer demand by identifying material shortages within the process.
The team recorded information using colored Kanban cards, which were then moved through various workstations in the production line. For example, a card might serve as an order form at one station and then become a shipping label at the next.
When implementing this system, Toyota adhered to several fundamental principles:
- Information is always passed from one process step to the next.
- Production does not begin without receiving a Kanban card.
- Each container in the production line must have a Kanban card specifying product details, production location, destination, and quantity.
- Containers must hold the exact specified quantity—no more, no less.
- Defective products or excess items are not passed to the next stage.
- The interval between deliveries and the number of Kanban cards should be minimized.
As a result, the Kanban cards allowed the team to control each stage of the production line tightly. Crucially, all these cards connected with the previous workflow and carried complete information.
Later, Taiichi Ohno and Toyota realized that Kanban principles were not limited to manufacturing and could be applied to any process or organization, which laid the foundation for the modern Kanban management method.
Kanban system at Toyota factory
How Kanban works
In today's applications, the Kanban model is based on several core principles:
- Visualize the workflow: Kanban utilizes boards, columns, and Kanban cards to visualize tasks and workflows. Remember the following text: Each card represents a task that needs to be completed. The columns on the board represent different stages of the workflow, indicating the various statuses of the tasks. A basic Kanban board typically consists of three columns: "To-do," "Doing," and "Done."
- Limit work in progress (WIP): Kanban restricts the number of tasks being worked on simultaneously at one stage. The number of tasks each person or department handles should also be limited to a manageable amount. This helps prevent overload and encourages individuals to focus on their current tasks rather than juggling multiple jobs simultaneously.
- Maintain a steady workflow: Kanban's goal is to optimize workflow, ensuring that tasks move smoothly from one stage to the next without unnecessary delays. Sequentially moving a Kanban card from one column to another helps prevent bottlenecks.
- Focus on continuous improvement: Even if a process is already highly efficient, there is always room for improvement. Continuous minor enhancements can lead to significant gains over time. For example, increasing productivity by 1% each week would result in a 67% increase over a year.
- Zero defects: The aim is to ensure that no defective products or errors are passed on to the next stage of the process.
2. Key concepts of Kanban
Kanban board
A Kanban board is a visual representation of the tasks within a project or workflow. Task cards move through columns that correspond to different stages in the workflow, representing the progress of tasks.
Additionally, the Kanban board can include supplementary information like performance charts, requirements, notes, or other diagrams to assist in managing and tracking work progress.
By looking at the Kanban board, team members can quickly grasp the roadmap toward the goal, the overall progress of the workflow, and critical information such as prioritized tasks, upcoming deadlines, and overdue tasks.
Kanban columns
Kanban columns describe sections of the Kanban board, with each section representing a different stage or status in the workflow. Task cards move through these columns as they progress through the workflow.
Each Kanban column contains a list (or collection) of task cards—typically those at the same workflow stage. In traditional project management tools, this is called a "to-do list" or "task list."
Kanban cards
Kanban task cards visualize tasks within the workflow. Each task card represents a specific task, such as a job to be completed or a product to be created. In traditional project management tools, this is a "to-do" or "task."
Each Kanban card typically includes the following information:
- Card title: A brief description of the task to be completed.
- Assigned person: The name of the person responsible for the task.
- Due date: The deadline or estimated time for task completion.
- Identifier number: A unique number assigned to each card for easy identification and tracking within the Kanban system.
- Color code or label: Indicators that show the status of the task or categorize the cards.
- Priority marker: An indicator to identify tasks that need to be prioritized.
Task cards serve as evidence of all activities leading to work results. Therefore, when it's necessary to review the entire workflow, the management team can quickly check each task card to gain a detailed and accurate overview.
3. Pros and Cons of Kanban
No method is flawless, and Kanban also has its strengths and weaknesses that are important to consider.
Benefits of Kanban
- Transparency: Kanban makes it easy for everyone to see all tasks and their responsibilities, bringing transparency to the entire workflow. This visibility allows team members to eliminate unnecessary tasks and focus on the most critical ones.
- Flexible work management: New Kanban cards can be easily added throughout the work process, and their status or priority can be adjusted. This flexibility makes Kanban a responsive model, helping the workflow adapt quickly to changing demands.
- Increased productivity: Kanban encourages people to focus on current tasks until they are completed, avoiding multitasking that can bottleneck the process or affect work quality. This principle leads to more organized and efficient task handling, significantly boosting productivity.
- Identification of bottlenecks: When working with a Kanban board filled with task cards, it becomes easy to spot bottlenecks: overloaded columns, tasks that have stagnated, or cards that haven’t progressed in a long time. This is one of the standout advantages of using visual management.
- Simple implementation: Thanks to its straightforward principles and easy set-up model, Kanban can be deployed in any team or organization, regardless of industry or size. It can even be flexibly applied to different processes or stages of a project without causing significant disruptions.
Disadvantages of Kanban
Difficulty in estimating time: Kanban focuses on continuous workflow without strict time constraints. The columns represent different stages but do not provide specific deadlines, making it challenging to plan when tasks will be done or estimate completion times.
Frequent updates required: Kanban requires users to update the status of task cards regularly, sometimes in real-time. If not done, the team risks working with outdated information, which undermines the purpose of visualizing the workflow through boards and columns.
Challenging at scale: The Kanban board can become cluttered in workflows with too many interconnected activities requiring frequent transitions. This can make it difficult for the team to track and manage all activities effectively.
Non-guaranteed output quality: While Kanban emphasizes task execution, it may pose risks to a broader picture—tasks may be completed, but the overall output or final product quality might not be ensured.
When to use Kanban?
Kanban is most suitable for projects where priorities frequently shift—sometimes daily—especially when the project has the following characteristics:
- Focusing on continuous workflow rather than specific, critical deadlines.
- Encountering backlogs due to stalled work, where the basic process is in place, and a smoother and more efficient operation is needed.
- There is no strict deadline for completion.
- Needing to flexibly add, remove, or edit task information during the workflow.
- Requiring continuous improvement throughout the process.
- The team is expected to report at any given time.
4. Comparing Kanban, Scrum, and Agile
The core difference
At its core, Agile is a methodology—a broad philosophy grounded in iterative and incremental project management principles. Agile aims to shorten product development cycles and deliver products to customers quickly.
Scrum is a management framework that adheres to the Agile methodology. It is commonly used in projects where the user does not fully define the end goal. Scrum focuses on optimizing value within fixed-time iterations, known as sprints, typically lasting from 1 to 4 weeks. This continuous cycle aims to improve the product, techniques, team dynamics, and work environment.
On the other hand, Kanban is a management model within the Agile family, providing specific tools and processes to implement Agile. It embodies many principles of Agile methodology, including adaptability to change and a strong emphasis on transparency across the team.
Therefore, the accurate comparison here is between Kanban and Scrum to highlight their differences:
Should you choose Kanban or Scrum?
Depending on the scale and nature of your project, you may apply either Kanban or Scrum. Both approaches promise to make the execution process more transparent, efficient, and continuously improved.
Alternatively, you could implement and manage your project using a hybrid model influenced by both Kanban and Scrum—known as Scrumban. Scrumban incorporates Scrum’s processes and Kanban’s visualization tools. For example, the Kanban board can be an excellent tool for tracking tasks within a Scrum sprint.
5. How to set up Kanban boards
Step 1: Outline your workflow on the Kanban board
Start by setting up either a physical whiteboard or an online Kanban board to implement Kanban. Next, break down your workflow into specific stages, from the beginning of the task to its completion. Draw columns on the board, each representing a stage in the workflow.
Step 2: Set WIP limits for each column
For Kanban to be effective, it’s crucial to establish Work In Progress (WIP) limits for each Kanban column—the maximum number of tasks allowed in that column at any given time. This step is vital to ensure a smooth workflow across the project and prevent work overload.
For individual workloads, limiting tasks to 2-3 at a time is also advisable. This helps maintain focus, reduces stress from multitasking, and ensures output quality.
Step 3: Create Kanban cards
Next, create a Kanban card for each task or activity and place them in the appropriate columns on the board. Each card should include essential details such as the title, person responsible, due date, and any additional relevant information.
You can arrange the cards in each column based on priority, with the most urgent tasks at the top. This allows for clear visibility of ongoing work and helps prioritize tasks effectively.
Consider using different colors for the cards to indicate various types of tasks, levels of urgency, or priority (e.g., red for urgent, yellow for medium priority, green for regular tasks).
Step 4: Start working
Once your Kanban board is set up, you can begin working on the tasks at the top of each column. After completing a task, move the card to the next column in the workflow. Adhering to the WIP limits is essential to avoid overload and optimize efficiency.
Address any issues or obstacles that arise during the process promptly to ensure the workflow remains as smooth as possible.
Step 5: Improve the Kanban system
Continuously gather feedback from your team and stakeholders (partners, customers, support staff) and use this information to improve the Kanban system. This includes refining the workflow, adjusting the board and column structure, or reorganizing and labeling Kanban cards.
Periodically, you can review and assess the status of the task cards, such as how many have moved to the final column, how many are overdue, etc. These metrics can help determine whether Kanban has effectively improved efficiency compared to the previous system.
Last words
The Kanban method and supporting software have significantly simplified task and workflow management. Kanban can be flexibly applied in various situations, whether at different times, locations, or scenarios, as long as the user has a systematic mindset and understands its principles.
On this page
- 1. What is Kanban?
- Definition of Kanban
- The history of Kanban
- How Kanban works
- 2. Key concepts of Kanban
- 3. Pros and Cons of Kanban
- Benefits of Kanban
- Disadvantages of Kanban
- When to use Kanban?
- 4. Comparing Kanban, Scrum, and Agile
- 5. How to set up Kanban boards
- Step 1: Outline your workflow on the Kanban board
- Step 2: Set WIP limits for each column
- Step 3: Create Kanban cards
- Step 4: Start working
- Step 5: Improve the Kanban system
- Last words